项目简介
博世智能制造解决方案长沙事业部从2015开始接触数字孪生并取得了从虚拟调试到仿真分析再到虚实互联等一系列的探索和开发,也进行了不同级别的丰富实践,同时还在博世强大工业领域的卓越平台上,继续深入这方面的研究和整合IOT,AI,ML 等关键技术。持续创新和提升,充分融合新一代信息技术助力装备数字化升级,实现装备软硬系统的自主可控,实现装备高质量发展、推动数字经济与实体经济融合发展。
工业数字孪生技术贯穿产品的全生命周期,从产品构想,设计研发,装配测试,到产线规划及调试,厂房布局均可通过数字孪生模型来实施验证优化,大幅减少产品的验证工作和降低了工期成本,实现产品和工程的精准控制与项目统一高效的管理。
项目特色
1、方案创新
基于客户端产线工艺设备布局、节拍要求、故障等数据,构建产线仿真模型。一方面,直观呈现系统建设方案和效果,便于方案沟通和评审,统一方案思想。另一方面,通过模拟生产与物流过程,计算分析仿真数据,获得反应车间系统效能指标,定位改善生产瓶颈,从而科学定量分析车间规划方案,并基于仿真试验和优化算法寻找更优的资源配置和生产策略等方案。
2、设计与生产创新
机电一体化同平台设计理念,Tool chain的应用与开发。通过重用现有知识与概念评估来帮助用户做出更明智的决策,不断提高机械设计的效率、缩短设计周期、降低成本、提升设计品质。
控制程序自动化生成设计方案。通过实际项目的操作,证明了机电一体化模块标准化方法以及相应的程序代码自动化生成方法的可行性与良好的结果效应。为程序设计的标准化、信息化提供了很好的方案,具备推广价值。
3、服务创新
教学和培训方式创新。装备的操作使用和维修采用实体操作的训练方式普遍存在成本高、难度大、风险高、周期长的缺点。利用虚拟调试技术,不依懒于具体的物理设备。将培训内容移植到虚拟设备上,运用3D模型立体展现机电设备的基本机构、工作流程。高度仿真的训练环境,能减少物理设备损耗、缩短培训周期、提高培训质量、降低培训成本、提高培训效率、增强培训深度、降低安全风险。
贯穿生产运行的全周期服务支持。从产品设计、工艺规划到制造工程、投入生产,再到运营服务、升级改造,数字孪生技术均发挥出重要作用。在工厂规划/升级阶段,开展车间规划方案的仿真定量评估和分析,科学的指导车间系统设计调整。在生产执行阶段,建立实时数据驱动的仿真机制,实现同步仿真运动和三维虚拟监控。
典型案例场景
复杂工艺单元虚拟调试
1、解决的问题:
依据设备工艺需求,开展工艺过程仿真,联动设备排查物理干涉,验证夹具设计结构;伺服同步控制仿真用以辅助工艺调试,以节约现场调试时间;在实体站上电前基于3D模型进行虚拟调试,验证软件程序质量的同时排查异常情况,整体有效缩短了约20%上电后调试时间。
2、验证情况:
仿真模型与PLC测试平台,虚实互通,在虚拟的世界里对模拟设备各部件之间的相互运动和电气行为进行仿真。仿真模型将速度、位置等信号反馈到PLC形成硬件在环仿真调试。
3、预期成效:
将虚拟调试引入产品工艺规划流程。针对焊接工艺,对焊点可达性、分配进行验真,工艺布局可行性分析,指导机器人选型,规划机器人焊接轨迹等;针对装配工艺,分别进行空间分析、动态仿真分析、人机工程分析;针对工艺设备,对重点工位,开展设备动作过程仿真,提前分析操作过程中可能存在的问题,给调试人员提供有力支持。
产线方案分析
1、解决的问题:
对整线产能、节拍以及各设备的利用率进行分析,提出多个方案比对,在不影响产能的前提下,最大化设备的利用率,优化绗车、WPC、AGV与Buffer位的数量和路径,减少成本投入的同时显著提升整线输出。
2、预期成效:
在现有设备基础上,帮助产能提升约20%
节约设备投资高达20%
减少库存和吞吐时间约20~60%
通过前期方案验证减低投资风险
最大限度的利用生产资源
提升生产线的设计和时间节点
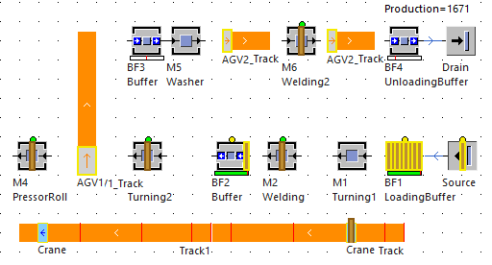
产线方案分析
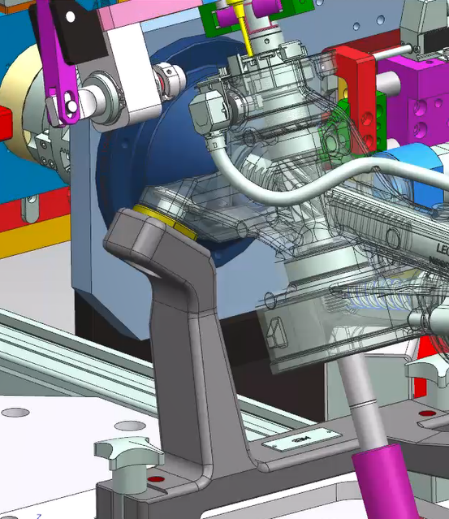
虚拟调试